Cáiliào rén bì zhī de ABS,PP,PC,PET děng 12 zhǒng sùliào de tèxìng, yòngtú jí gōngyì!
35 / 5,000
Materials professionals must know the properties, uses and processes of 12 types of plastics, including ABS, PP, PC, PET, etc.!
Acrylonitrile-butadiene-styrene (ABS) is a thermoplastic synthetic polymer resin with a good balance of properties that can be tailored to suit specific needs. Its main physical properties are: hard and strong. Resin grades of ABS can bend like elastomer (or rubber). Among them, polybutadiene provides good compressive strength, non-crystalline styrene thermoplastic makes ABS processing easier (easier to flow in the mold), and acrylonitrile increases ABS's fastness, hardness and corrosion resistance.
Effective control of these three components allows designers to design the degree of elasticity according to the needs of the final product. Perhaps because of this, ABS is widely used in household products and white products. Although it is not as tough as other engineering polymers, it can effectively control costs.
Material characteristics:
It can maintain good compressive strength even at low temperatures. High hardness, high mechanical strength, good wear resistance, light specific gravity, relative thermal index up to 80c, and good dimensional stability at high temperatures. Fireproof, simple processing, good gloss, easy to color, and relatively low cost compared to other thermoplastics. Low cost, multiple production methods, good chemical resistance, high surface hardness, scratch resistance, good structural stability, high pressure resistance, excellent structural strength and hardness.
Typical uses: electronic consumer products, toys, environmentally friendly products, car dashboards, door panels, outdoor guardrails.
Main processes: steel mold injection casting, injection molding, TPO injection molding
2. Polypropylene (PP)
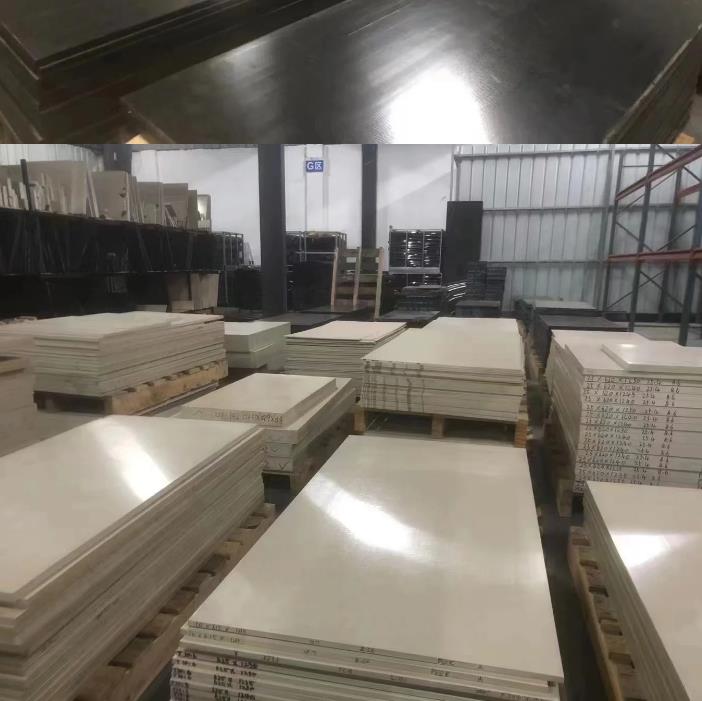
The design work of PP is not limited to creating beautiful shapes and perfect functions, but often looking for ways to reduce the price and processing costs of single products while avoiding mass production. Simply put, it is to find a product that is suitable for mass production; using mass production to reduce the cost of each unit, while not requiring high investment and high output to meet mass production.
It is widely used in all aspects of product design, from packaging, lighting equipment to indoor supplies. However, people have not been able to fully apply this material through the thermoforming process.
Material characteristics:
A variety of transparency and color options, low density, strong heat resistance, good balance of hardness, fastness and strength, simple and flexible processing methods, excellent resistance to chemicals
Typical uses: furniture, packaging, lighting equipment, food packaging, table mats, folders, note boxes
Main process: injection molding
3. Polymethyl methacrylate (PMMA)
Acrylic acid began to be developed in the 1930s, when it was mainly used for top turning devices of safety glass. Acrylic material was first registered as the well-known organic glass in 1934. The perfect combination of transparency and lightness made it an interesting new plastic. By the 1960s, the material was discovered by avant-garde furniture designers and used in interior environments such as modern furniture.
Since acrylic is available in a variety of colors, its function naturally expanded from lighting equipment to the manufacture of company logos. All international brands now use this material for signage. Acrylic has a hard surface and can be easily mistaken for glass from a distance. It can be made into thin sheets by casting and extrusion to meet the requirements of different applications. Cast acrylic sheets can be used as high-quality glass and are suitable for mass production.
The high molecular weight makes it very strong, flexible and easy to handle and manufacture. This casting method is particularly ideal for large products and small batches of coloring. Extruded sheets have a light molecular weight, so they are easy to pump into shape. The extrusion process makes the product have excellent thickness resistance and is also very cheap for large-scale productionMaterial characteristics
:
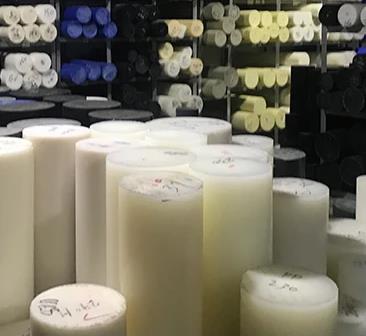
A variety of manufacturing and processing methods, easy processing A variety of transparent, translucent and opaque and color, surface effects to choose from, excellent resistance to chemicals and weathering, high printing adhesion, fully recyclable, excellent visual clarity, special color creativity and color matching, high surface hardness, good durability.
Typical uses: display retail signs, indoor supplies, furniture, lighting equipment, glass assembly.
4. Cellulose acetate (CA)
Cellulose acetate products have a warm touch, sweat resistance, and can self-luminous. It is a traditional polymer with bright colors and syrup-like transparency. It has been developed since the early 20th century, even earlier than insulating Bakelite. Because of its marble-like effect, cellulose acetate can often be used in products such as tool handles, eyeglass frames and hairpins, so it is also one of the most easily recognized polymers.
As a material for hand tools, it can combine its excellent pressure resistance with a good feel. Other materials, such as polypropylene, have better pressure resistance but feel more slippery. The self-brightening component of cellulose acetate material comes from its softness, and slight scratches on the surface can be polished off. It contains cotton and wood (cellulose) components and can be molded by injection casting, transfer casting and extrusion. You can also buy it in thin sheets.
Material characteristics:
Low thermal conductivity, flexible production, multiple visual effects, excellent fluidity, good surface gloss, good electrical insulation, anti-static, self-brightness, high transparency, strong pressure resistance, unique surface vision, recyclable material
Typical uses: tool handles, hairpins, toys, goggles and helmets, glasses frames, toothbrushes, cutlery handles, combs, photo negatives
Main process: steel mold injection casting
5. Polyethylene terephthalate (PET)
PET is usually used for packaging food and soft drinks. However, PET is not suitable for beer because beer is heat-sensitive to oxygen and carbon dioxide. Plastic bottles have a total of 5 layers, and the two layers sandwiched between the main layer of PET are oxygen decay products that can prevent oxygen from entering and exiting. Miller Brewing Company, which produced the first plastic beer bottle in 2000, claims that plastic bottles keep beer cooler than aluminum cans and even as well as glass bottles. They are resealable and not easily broken.
Material properties:
Recyclable (PET is one of the most recyclable plastic resins), excellent chemical resistance, hard and durable, excellent surface finish, good compression resistance
Typical uses: food packaging, electronic products, soft drink bottles, Miller beer bottles
Main process: injection molding and blow molding
6. Polyvinyl chloride (PVC)
PVC may be one of the most widely used plastic materials, from plastic doors and windows in daily life to water pipes, gutters, shoes, cable insulation, toys, injection molded products, bright bodies, extruded products, glass assemblies, packaging, credit cards, etc. It can be found almost everywhere, and PVC material is also one of the cheaper plastic materials.
Material properties:
Elastic, easy to color, with a variety of hardness options, can be extruded, injection-casted and blow-molded, can be reinforced with glass fiber, can maintain its properties at low temperatures, can be printed, recycled, good tear and abrasion resistance, good sun and seawater resistance, good oil and chemical resistance
Main process: injection casting, blow molding or extrusion molding
7. Polyurethane Technoge (PU)
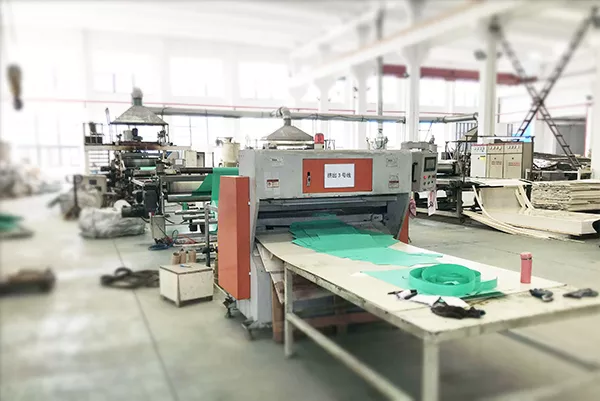
A skin-like material that breathes and stretches, but can be molded to any thickness. These properties were first used in the medical and orthopedic industries as cushions for hospital patients. Technoge is one of the materials that has been applied experimentally to new and more general interior products.
Technoge is a combination of liquid and solid. The product can be obtained by pouring the liquid into a mold, which means that other substances can be easily added to it. In the sheet state, the shape of the material can be obtained by stamping or cutting. The advantage over water or silicone gels is that it does not contain plasticizers, which means that the material is less likely to lose its basic properties over a long period of time. It is the only gel that does not crack, harden or age.
Material properties:
Good pressure dissipation, breathable (good absorption and release), strong recovery ability, easy to mix with decorative materials, strong shock absorption, strong pressure absorption, adjustable hardness, high elasticity, non-fading, stickable, non-irritating to the skin, injection casting
Typical uses: bicycle seats, orthopedic seat cushions, insoles, office chairs, tennis racket handles
Main processes: injection casting, embossing, cutting
8. Silicone polymer
In 1943, a Scottish engineer, James Wright, experimented with mixtures in test tubes in the General Electric Company laboratory in Connecticut, USA. He accidentally mixed boric acid and silicone oil together and made them "polymerize". When Wright sucked this adhesive agent from the test tube, he threw some on the ground. Amazingly, the substance bounced off the floor, and elastic oil mud was born.
Wright decided to find a practical use for his invention, and finally, SillPuttyTM was introduced at the International Toy Fair in New York in 1950. After persistent efforts, some large toy distributors decided to distribute SillPuttyTM, and the rest is history.
Material properties:
Gradually flattened under the earth's gravity, 80% bounce (relative to the position of being thrown), an expanding compound, solid and maintains its shape when pressure is applied quickly; liquid and easy to mold when pressure is applied gradually, cooling can increase bounce, can float on the water when made into a boat shape, sinks when made into a sphere, non-toxic, non-irritating, highly elastic, and available in a variety of colors.
Typical use: No other applications for the time being
9. Polycarbonate (PC)
As a modern material, the use of polycarbonate in this product is to interpret a typical object and shape. The direct reference for this design may be the wooden ladder found in your grandmother's basement. Instead of wood, this product is made of another modern material that is perfectly suited to this function.
Polycarbonate is as hard as other polymers, but also lightweight and can be provided in a variety of colors and post-processing effects. As a relatively young member of the thermoplastic family, polycarbonate, like many other plastic materials, was accidentally discovered by General Electric (GE) in the early 1950s. This material is known for its ultra-clearness and ultra-strongness, and is often used as a substitute for glass in transparent, smooth and other applications.
Material characteristics:
It can provide a range of colors with good clarity, simple processing procedures, very good impact resistance, and can provide fully transparent, translucent and opaque appearance effects. Even at high temperatures, it has strong dimensional stability, high temperature resistance up to 125C, fireproof, radiation-proof, durable, recyclable, non-toxic
Typical uses: safety helmets, glasses, lightweight CD boxes, kitchen utensils, computer housings, architectural glass windows, mobile phone housings
Main process: injection molding
10. Phenolic esters
Abbott Laminette was established in Bra, Italy in 1957. Since then, the company has been at the forefront of innovation in the production of various sheets, including DIAFOS in 1987, the first transparent sheet material. The company has collaborated with some of the most famous designers of the 20th century, including Memphis and Alchemia Design Studio, and is known for its exploration of surface textures. "Color Layer" is a unique product produced by Abbott Laminet that explores the functionality and visual artistry of the edge of the product.
The sheet is composed of two layers of material and has a standard thickness. The middle part is composed of multiple layers of paper filled with aminoplast resin. The surface is made of decorative paper filled with melamine formaldehyde resin. Abbott uses the decorative layer as the core material of the "Color Layer" product. The edges of the product can be sanded to obtain unique edge details.
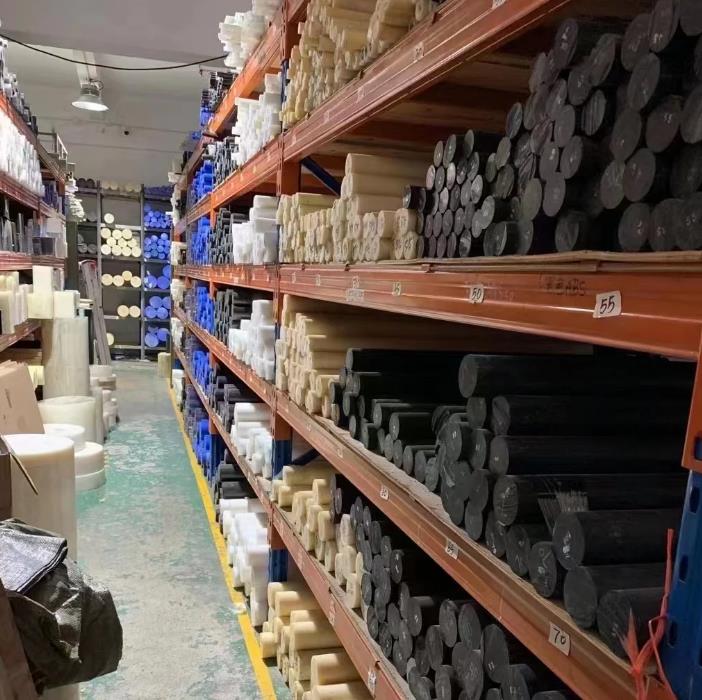
Material properties:
Higher friction resistance, higher impact resistance, excellent moisture resistance, easy adhesion, good water and water vapor resistance, easy to clean, good dimensional stability, strong hard wear resistance, strong decorative edge surface, more economical than other materials with harder surfaces
Typical uses: office furniture, indoor and outdoor paneling, flooring, street equipment, work surfaces
11. Polystyrene (PS)
Like many polymers, polystyrene was discovered accidentally. Styrene was discovered in the mid-19th century, but it was not commercially developed until the 1930s. Other polymers in the styrene family include ABS, SAN, SMA and ASA. Today, it is one of the most widely used plastic raw materials.
Material properties:
Good clarity, high strength, simple process, easy to color, cheaper than other polymers, high transparency, strong water and moisture resistance, strong dimensional stability
Typical uses: packaging, toys, hangers, household products, electronic products, mold boxes, disposable cups
12. Artificial rubber (TPE)
TPE has the processing properties of thermoplastics and feels like rubber. TPE is a genus of the thermoplastic synthetic rubber family, including TPO (thermoplastic paraffin) and TPS (thermoplastic styrene). These are engineering polymers that can provide toughness and hardness in most cases. TDE is usually molded by injection casting, blow molding or extrusion molding.
Material properties: elastic, easy to color, with a variety of hardness options, can be extruded, injection-cast and blow-molded, can be reinforced with glass fiber, can maintain its properties at low temperatures, can be printed and recycled, good tear and abrasion resistance, good sun and seawater resistance, good oil and chemical resistance